Bearing data
Main dimensions
The main dimensions are the key dimensions of a rolling bearing. They include ➤ Figure:
- the bore diameter (d)
- the outside diameter (D)
- the width or height (B, C, T or H)
- the chamfer dimensions (r)
Main dimensions
|
![]() |
Standardised and non-standardised dimensions
External dimensions are standardised
The dimensions which determine the installation space are standardised. Standardisation is not, however, applied to the internal dimensions, such as the size and quantity of the rolling elements for example. The main dimensions of metric rolling bearings are defined in the following ISO dimension plans:
- ISO 15:2017 for radial rolling bearings, excluding single row needle roller bearings, insert bearings and tapered roller bearings
- ISO 355 : 2007 for tapered roller bearings
- ISO 104 : 2015 for axial bearings
DIN 616 describes dimension plans for radial and axial bearings. An overview of ISO and DIN rolling bearing standards is given in DIN 611:2010-05.
ISO dimension plans
Standard dimensions
Experience has shown that the predominant proportion of all bearing arrangement tasks can be fulfilled using bearings with standard dimensions, which are contained in ISO dimension plans.
Advantages of dimension plans
The dimension plans are valid for different bearing types. Standard rolling bearings of different types can thus be manufactured to the same external dimensions. As a result, a designer working on the same design envelope can make a selection between bearings of several types with the same external dimensions.
Several outside diameters/ width dimensions are assigned to one bearing bore
In the dimension plans, one bearing bore is allocated several outside diameters and width dimensions. In this way, it is possible to design several bearings of the same type that, for the same bore, exhibit different load carrying capacities. The development of new bearing series and individual new rolling bearings in accordance with the dimension plans has considerable advantages for users and manufacturers.
Width and diameter series
Bearing series are described using numbers
Width and diameter series are described using numbers. In the case of radial bearings in accordance with DIN 616 and ISO 15, these are as follows:
- for width series, the numbers 8, 9, 0, 1, 2, 3, 4, 5, 6, 7 ➤ Figure
- for the identification of diameter series, the numbers 7, 8, 9, 0, 1, 2, 3, 4, 5 ➤ Figure
Identification of width series For radial bearings to DIN 616 and ISO 15
|
![]() |
Identification of diameter series For radial bearings to DIN 616 and ISO 15
|
![]() |
Dimension series
The dimension series is created from the width series and the diameter series
The specific number of the width and diameter series, when combined, identifies the dimension series ➤ Table. When this table is used, for example, for a radial bearing of the width series 2 and the diameter series 3, this gives the dimension series 23 ➤ Table and ➤ Figure. If the bearing bore code is then added, ➤ section, the bearing size is completely defined.
Dimension series for radial bearings (excluding tapered roller and needle roller bearings)
Width series – |
|||||||||||
---|---|---|---|---|---|---|---|---|---|---|---|
8 |
9 |
0 |
1 |
2 |
3 |
4 |
5 |
6 |
7 |
||
Diameter series – |
5 |
‒ |
‒ |
‒ |
‒ |
‒ |
‒ |
‒ |
‒ |
‒ |
‒ |
4 |
‒ |
‒ |
04 |
‒ |
24 |
‒ |
‒ |
‒ |
‒ |
‒ |
|
3 |
83 |
‒ |
03 |
12 |
23 |
33 |
‒ |
‒ |
‒ |
‒ |
|
2 |
82 |
‒ |
02 |
12 |
22 |
32 |
42 |
52 |
62 |
‒ |
|
1 |
‒ |
‒ |
01 |
11 |
21 |
31 |
41 |
51 |
61 |
‒ |
|
0 |
‒ |
‒ |
00 |
10 |
20 |
30 |
40 |
50 |
60 |
‒ |
|
9 |
‒ |
‒ |
09 |
19 |
29 |
39 |
49 |
59 |
69 |
‒ |
|
8 |
‒ |
‒ |
08 |
18 |
28 |
38 |
48 |
58 |
68 |
‒ |
|
7 |
‒ |
‒ |
‒ |
17 |
27 |
37 |
47 |
‒ |
‒ |
‒ |
Generation of the dimension series
|
![]() |
Dimension plan for metric tapered roller bearings to ISO 355
Tapered roller bearings can generally also be classified in the dimension plans to ISO 355 ➤ Figure. The dimension series are designated in these by a combination of three symbols, e. g. 3FE ➤ Figure.
Dimension plan for tapered roller bearings (excerpt) to ISO 355
|
![]() |
Designation system
Clear designation
Each rolling bearing has a designation that clearly indicates the type, dimensions, tolerances and internal clearance, if necessary with other important features.
Interchangeability
Bearings that have the same standardised designation are interchangeable with each other. In the case of separable bearings, it cannot always be ensured that individual parts with the same origin can be interchanged with each other.
In Germany, the bearing designations are standardised in DIN 623-1. These designations are also used in many other countries.
Designation
The designation is a code comprising numbers and letters
The designation for the bearing series comprises numbers and letters or letters and numbers. It indicates the type of bearing, the diameter series and, in many cases, the width series too ➤ Figure, ➤ Figure and ➤ Figure. The diameter and width series are described in ➤ section.
Basic designation, prefix and suffix
Basic designation
The basic designation contains the symbols for the bearing series and the bearing bore ➤ Figure, ➤ Figure and ➤ Figure.
Prefix
The prefix normally identifies individual bearing parts of complete bearings (in certain cases, this may also be part of the basic designation) ➤ Figure and ➤ Figure.
Suffix
The suffix defines special designs and features ➤ Figure and ➤ Figure. The prefix and suffix describe other features of the bearing but are not standardised in all cases and may vary in use depending on the manufacturer.
Designations – examples
Examples of the composition of designations on the basis of their definition in accordance with ➤ Figure are shown on ➤ Figure.
Composition of designations |
![]() |
Examples of bearing designations, constructed in accordance with ➤ Figure
|
![]() |
Designations of metric tapered roller bearings according to ISO 355 and ISO 10317
Structure of bearing designation for metric tapered roller bearings
➤ Figure describes as an example the structure of the designation for a metric tapered roller bearing (dimension series to ISO 355, designation to ISO 10317). The 3 indicates the contact angle range. The first letter (F in this case) indicates a diameter series. Each diameter series has a certain ratio D/d (outside diameter to bore diameter). The second letter (E in this case) indicates a width series. Each width series has a certain ratio of bearing width T to the height of the bearing cross-section. The addition of the letter T (for tapered roller bearing) at the start and a three-digit number at the end for the bearing bore diameter in mm (in this case 120) gives the complete designation of a tapered roller bearing (e. g. T3FE 120 ➤ Figure).
DIN 720 Appendix 1 gives an interchange table for DIN and ISO designations.
Composition of designation for metric tapered roller bearings to ISO 10317 Dimension series to ISO 355, designation to ISO 10317 |
![]() |
Example designation for metric tapered roller bearings to DIN 720 |
![]() |
Bearing designations in accordance with DIN 623-1:1993 – basic designation structure |
![]() |
Determining the bearing bore
For d < 10 mm, the bore diameter is stated in the basic designation
For certain bearing types, the bearing bores are stated directly or in an encoded form in accordance with DIN 623-1. Up to d < 10 mm, the bearing bore diameter is specified in the dimension-specific part of the designation (basic designation) directly as a number indicating the diameter ➤ Figure.
Example
Deep groove ball bearing 623, bore diameter = 3 mm.
Bore code
The bore code describes the bearing bore from d ≧ 10 mm
For nominal dimensions d ≧ 10 mm to d < 500 mm, the diameter is described by means of a bore code ➤ Figure.
For bores from 10 mm to 17 mm, the following applies:
- d = 10 mm, bore code 00
- d = 12 mm, bore code 01
- d = 15 mm, bore code 02
- d= 17 mm, bore code 03
For all rolling bearings in the range from d = 20 mm to d = 480 mm (excluding double direction axial bearings), the bore code is formed by dividing the dimension of the bearing bore by 5.
Example
Bearing bore d = 360 mm divided by 5 (360 : 5), bore code = 72.
From d > 480 mm
From d > 480 mm, the unencoded bore diameter is given with an oblique after the bearing series, e.g. 618/500 with bore diameter d = 500 mm.
Intermediate sizes
The intermediate sizes, such as bore diameter d = 22, 28 and d = 32 mm for example, are also given with an oblique as /22, /28 and /32.
Magneto bearings
In the case of magneto bearings, the unencoded nominal bore dimension is given.
Radial internal clearance
The radial internal clearance is determined on the dismounted bearing
The radial internal clearance applies to bearings with an inner ring and is determined on the unmounted bearing. It is defined as the amount by which the inner ring can be moved in a radial direction from one extreme position to the other in relation to the outer ring ➤ Figure.
The radial internal clearance groups are defined in DIN 620-4 and ISO 5753-1 and are described in DIN 620-4 by means of codes that comprise the capital letter C and a number. ISO 5753-1 designates the groups by the word "Group" and a number ➤ Figure and ➤ Table.
Internal clearance groups C2, CN, C3, C4, C5 = radial internal clearance groups according to DIN 620-4 Group 2, N, 3, 4, 5 = radial internal clearance groups according to ISO 5753-1 |
![]() |
Radial internal clearance groups
Internal clearance group |
Description |
Application |
|
---|---|---|---|
DIN 620-4 |
ISO 5753-1 |
||
C2 |
Group 2 |
Internal clearance < CN |
For heavy alternating loads combined with swivel motion |
CN |
Group N |
Normal internal clearance, CN is not included in bearing designations |
For normal operating conditions with shaft and housing tolerances |
C3 |
Group 3 |
Internal clearance > CN |
For bearing rings with press fits and large temperature differential between the inner and outer ring |
C4 |
Group 4 |
Internal clearance > C3 |
For bearing rings with press fits and large temperature differential between the inner and outer ring |
C5 |
Group 5 |
Internal clearance > C4 |
For bearing rings with press fits and large temperature differential between the inner and outer ring |
Enveloping circle
For bearings without an inner ring, the enveloping circle Fw is used. This is the inner inscribed circle of the rolling elements in clearance-free contact with the outer raceway ➤ Figure.
Enveloping circle Fw = enveloping circle diameter
|
![]() |
Operating clearance
The operating clearance is determined on a bearing still warm from operation
The operating clearance is determined on a mounted bearing still warm from operation. It is defined as the amount by which the shaft can be moved in a radial direction from one extreme position to the other.
The operating clearance is derived from the radial internal clearance and the change in the radial internal clearance as a result of interference fit and thermal influences in the mounted condition.
A normal operating clearance is usually achieved with internal bearing clearance CN
The operating clearance value is dependent on the operating and installation conditions of the bearing. A larger operating clearance is, for example, necessary if heat is transferred via the shaft, the shaft undergoes deflection or if misalignment occurs. An operating clearance smaller than CN should only be used in special cases, for example in high precision bearing arrangements. Normal operating clearance is achieved with an internal clearance of CN or, for larger bearings, more usually C3 if the recommended shaft and housing tolerances are maintained.
Calculation of operating clearance
The operating clearance is determined in accordance with ➤ Equation.
Operating clearance

Legend
s | μm |
Radial operating clearance of mounted bearing warm from operation |
sr | μm |
Radial internal clearance |
ΔsP | μm |
Reduction in radial internal clearance due to fit |
ΔsT | μm |
Reduction in radial internal clearance due to temperature |
Reduction in radial internal clearance due to fit
The radial internal clearance is reduced due to the fit as a result of expansion of the inner ring and contraction of the outer ring ➤ Equation.
Reduction in radial internal clearance
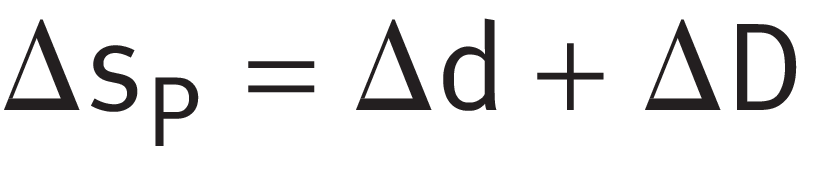
Legend
ΔsP | μm |
Reduction in radial internal clearance due to fit |
Δd | μm |
Expansion of the inner ring |
ΔD | μm |
Contraction of the outer ring |
The expansion of the inner ring is calculated in accordance with ➤ Equation.
Expansion of the inner ring

Legend
d | mm |
Bore diameter of the inner ring |
U | μm |
Theoretical interference of the fitted parts with firm seating. The theoretical oversize of the fitted parts with a firm seating is determined from the mean deviations and the upper and lower deviations of the tolerance zones of the fitted parts reduced by 1/3 of their acceptable value. The amount of surface smoothing during assembly must be subtracted from this. |
F | mm |
Raceway diameter of the inner ring |
For very thin-walled housings and light metal housings, the reduction in the radial internal clearance must be determined by mounting trials.
The contraction of the outer ring is calculated in accordance with ➤ Equation.
Contraction of the outer ring

Legend
ΔD | μm |
Contraction of the outer ring |
E | mm |
Raceway diameter of the outer ring |
D | mm |
Outside diameter of the outer ring |
Reduction in radial internal clearance due to temperature
The radial internal clearance can alter considerably if there is a substantial temperature differential between the inner and outer ring ➤ Equation.
Reduction in radial internal clearance due to temperature

Legend
ΔsT | μm |
Reduction in radial internal clearance due to temperature |
α | K-1 |
Coefficient of thermal expansion of steel: α = 0,000011 K-1 |
dM | mm |
Mean bearing diameter (d + D)/2 |
ϑIR | °C, K |
Temperature of the inner ring |
ϑAR | °C, K |
Temperature of the outer ring (usual temperature difference between inner and outer ring: 5 K to 10 K) |
A larger radial internal clearance should be used for shafts running at high speeds, since adequate thermal compensation between the bearing, shaft and housing does not occur in this situation. ΔsT can, in this case, be significantly higher in this case than for continuous operation.
Axial internal clearance
The axial internal clearance sa is defined as the amount by which one bearing ring can be moved relative to the other, without load, along the bearing axis ➤ Figure.
Axial internal clearance in comparison with radial internal clearance sa = axial internal clearance sr = radial internal clearance |
![]() |
Relationship between radial and axial internal clearance
With various bearing types, the radial internal clearance sr and the axial internal clearance sa are dependent on each other. Guide values for the correlation between radial and axial internal clearance are shown for some bearing types ➤ Table.
Correlation between axial internal clearance and radial internal clearance
Bearing type |
Ratio between axial and radial internal clearance sa/sr |
|
---|---|---|
Self-aligning ball bearings |
2,3 · Y01) |
|
Spherical roller bearings |
2,3 · Y01) |
|
Tapered roller bearings |
Single row, arranged in pairs |
4,6 · Y01) |
Tapered roller bearings |
Matched pairs (DF) |
2,3 · Y01) |
Angular contact ball bearings |
Double row, series 32 and 33 |
1,4 |
Angular contact ball bearings |
Double row, series 32..-B and 33..-B |
2 |
Four point contact bearings |
1,4 |
- Y0 = axial load factor in accordance with product table.
If the operating clearance is an important design criterion, please consult Schaeffler.
The calculation module BEARINX Shaft Calculation, which is available from Schaeffler free of charge, can be used to calculate and analyse the operating clearance.
Calculation example
Example: deep groove ball bearing 6008-C3
For deep groove ball bearings, the calculation of the axial internal clearance is shown in the following example:
Deep groove ball bearing | 6008-C3 | |
Bore diameter d | 40 mm | |
Radial internal clearance before fitting | 15 μm to 33 μm | |
Actual radial internal clearance | 24 μm | |
Mounting tolerance | Shaft | k5 |
Housing | j6 | |
Reduction in radial internal clearance during fitting | 14 μm | |
Radial internal clearance after fitting / | 24 μm - 14 μm = 10 μm | |
Ratio sa / sr | 13 |
Axial internal clearance
-
sa = 13 · 10 μm = 130 μm
Approximate calculation of the ratio of radial to axial internal clearance for deep groove ball bearings sa = axial internal clearance sr = radial internal clearance d = bearing bore diameter
|
![]() |
Bearing materials
Standard steels
Schaeffler rolling bearings fulfil the requirements for fatigue strength, wear resistance, hardness, toughness and structural stability. The material used for the rings and rolling elements is generally a low-alloy, through hardening chromium steel of high purity. For bearings subjected to considerable shock loads and reversed bending stresses, case hardening steel is also used (supplied by agreement). The results of research as well as practical experience confirm that bearings made from the steel currently used as standard can achieve their endurance limit if loads are not excessively high and the lubrication and cleanliness conditions are favourable.
High Nitrogen Steel
For the most challenging conditions
Through the use of special bearings made from HNS (High Nitrogen Steel, supplied by agreement), it is possible to achieve adequate service life even under the most challenging conditions (high temperatures, moisture, contamination).
High performance steels Cronidur and Cronitect
Steels for increased requirements
For increased performance requirements, highly corrosion-resistant, nitrogen-alloyed martensitic HNS steels are available, such as Cronidur and Cronitect.
In contrast to Cronidur, the more economical alternative Cronitect has nitrogen introduced into the structure by means of a surface layer hardening process.
Both steels are clearly superior to conventional corrosion-resistant steels for rolling bearings in terms of corrosion resistance and fatigue strength.
Ceramic materials
Hybrid bearings
Ceramic hybrid spindle bearings contain balls made from silicon nitride. These ceramic balls are substantially lighter than steel balls. The centrifugal forces and friction are significantly lower.
Hybrid bearings allow very high speeds, even with grease lubrication, as well as long operating life and low operating temperatures.
Materials and bearing components
Suitable materials and their use in rolling bearing technology ➤ Table.
Materials and bearing components
Material |
Bearing components (example) |
---|---|
Through hardening chromium steel – |
Outer and inner ring, axial washer |
HNS – High Nitrogen Steel |
Outer and inner ring |
Corrosion-resistant steel – |
Outer and inner ring |
Case hardening steel |
For example, |
Flame or induction hardening steel |
Roller stud of stud type track rollers |
Steel strip to EN 10139, SAE J403 |
Outer ring for drawn cup |
Silicon nitride |
Ceramic balls |
Brass alloy |
Cage |
Aluminium alloy |
Cage |
Polyamide (thermoplastic) |
Cage |
NBR, FKM, TPU |
Sealing ring |
Corrosion protection by Corrotect
Rolling bearings are not resistant to corrosion by water or agents containing alkalis or acids but are often exposed to these corrosion-inducing agents. In these applications, corrosion protection is therefore a decisive factor in achieving a long operating life of the bearings.
In principle, corrosion-resistant steels to ISO 683-17 can be used. These bearings have the prefix S. For higher requirements, it may be advisable to use the high performance steels Cronidur and Cronitect.
Corrotect coating
Special coatings
An extensive modular coating concept currently offers a wide range of surface improvements aimed at increasing the performance and rating life of bearing components. The “added value in the form of coatings” thus provided, is now established as a standard procedure for a wide variety of Schaeffler components.
Various coating variants and coating thicknesses
Thin anti-corrosion coating systems of 0,5 μm – 3 μm and 2 μm – 5 μm are available for bearing applications. Various Corrotect variants with coating thicknesses > 5 μm also exist, which can be applied as necessary. The Corrotect coatings thus offer corrosion protection times – as a function of the coating variant and coating thickness – of ≧ 720 h against base metal corrosion (in accordance with DIN EN ISO 9227).
Cr(VI)-free coatings
Systems are free from Cr(VI), provide effective protection against corrosion and, as result, extend the useful life of Schaeffler components. In isolated cases, the dimensional changes brought about by the coating must be taken into account in a further processing operation.
Detailed information on the modular coating concept and individual coating systems can be found in Technical Product Information TPI 186 “Higher Performance Capacity Through the Use of Coatings”. This publication can be requested from Schaeffler.
Advantages of Corrotect thin coating
The advantages of the special coating Corrotect are all-round corrosion protection, including the turned surfaces of chamfers and radii ➤ Figure. It also gives long-term prevention of rust penetration beneath seals and smaller bright spots are protected against corrosion by the cathodic protection effect. In comparison with uncoated parts, operating life is significantly increased by the corrosion protection. There is no decrease in load carrying capacity (such as occurs in the use of corrosion-resistant steels). It is therefore theoretically possible to replace uncoated bearings by coated bearings of the same dimensions. However, it is advisable to check the suitability for the specific application in advance since, for example, abrasion may occur. During storage, there is no need to use organic preservatives.
Mounting of Corrotect-coated bearings
Before bearings with Corrotect coating are mounted, compatibility with the media should always be checked.
For lower press-in forces, the surface of the parts should be lightly greased, the tolerances are increased by the thickness of the coating.
Coated and uncoated part after a salt spray test Test time 24 h in salt spray
|
![]() |
Cages
The functions of cages
Cage is a retainer with pockets for the rolling elements
Cage pockets, which are separated from each other by bars and are uniformly distributed around the circumference of the cage, maintain the spacing of the rolling elements relative to each other and ensure the distribution of load. In addition, the bars prevent sliding friction between adjacent rolling elements and guide the rolling elements parallel to the bearing axis in the load-free zone. In the case of cylindrical and needle roller bearings, they additionally prevent skewing of the rolling elements by guiding the rolling elements parallel to the bearing axis.
Cages ensure spacing between the rolling elements, even in the load-free zone
In the load-free zone, the rolling elements are no longer driven by the inner or outer ring. As a result, they fall behind relative to the direction of rotation of the rings. Cages ensure that the spacing between the rolling elements is maintained, even in the load-free zone.
Where bearings are separable and can be swivelled, the rolling elements cannot escape from the bearing
In the case of bearings that are separable and can be swivelled, such as tapered roller, spherical roller and some cylindrical roller bearings, cages prevent rolling elements from falling out of the bearing. The rolling element set and cage can thus be mounted and dismounted as a complete unit.
Sheet metal or solid section cages
Sheet metal cages
Rolling bearing cages are subdivided into sheet metal and solid section cages. The cages are predominantly made from steel and, for some bearings, from brass ➤ Figure. In comparison with solid section cages made from metal, sheet metal cages are of lower mass. Since a sheet metal cage only fills a small proportion of the gap between the inner and outer ring, lubricant can easily reach the interior of the bearing and is held on the cage. In general, a sheet steel cage is only included in the bearing designation if it is not defined as a standard version of the bearing.
Solid cages
These cages are made from metal, laminated fabric or plastic ➤ Figure. They can be identified from the bearing designation.
Solid cages made from metal or laminated fabric
Solid cages made from metal are used where there are requirements for high cage strength and at high temperatures. Solid cages are also used if the cage must be guided on ribs. Rib-guided cages for bearings running at high speeds are made in many cases from light materials, such as light metal or laminated fabric, in order to achieve low inertia forces.
Solid cages made from polyamide PA66
Solid cages made from polyamide PA66 are produced using the injection moulding process ➤ Figure. As a result, cage types can generally be realised that allow designs with particularly high load carrying capacity. The elasticity and low mass of polyamide are favourable under shock type bearing loads, high accelerations and decelerations and tilting of the bearing rings in relation to each other. Polyamide cages have very good sliding and emergency running characteristics.
Cages made from glass fibre reinforced polyamide PA66 are suitable for continuous temperatures up to +120 °C. For higher operating temperatures, plastics such as PA46 or PEEK can be used.
When using oil lubrication, additives in the oil can impair the cage operating life. Aged oil can also impair the cage operating life at high temperatures, so attention must be paid to compliance with the oil change intervals.
Cage designs
Proven cage designs ➤ Figure to ➤ Figure.
Sheet steel cages
|
![]() |
Solid brass cages
|
![]() |
Solid cages made from glass fibre reinforced polyamide
|
![]() |
Guidance of cages
The cages are guided by rolling elements or ribs
A further means of distinguishing between cages is their guidance method ➤ Figure. Most cages are guided by the rolling elements and do not have a suffix for the guidance method. If guidance is by the bearing outer ring, the suffix A is used. Cages that are guided on the inner ring have the suffix B.
Standard cages are suitable under normal operating conditions
Under normal operating conditions, the cage design defined as the standard cage is generally suitable. Standard cages, which may differ within a bearing series according to the bearing size, are described in the product chapters. Under special operating conditions, a cage that is suitable for the specific conditions must be selected.
Guidance of cages
|
![]() |
Operating temperature
Standard rolling bearings can be used up to +120 °C
Rolling bearings are heat treated such that, depending on the bearing type, they are generally dimensionally stable up to +120 °C (certain bearings up to +150 °C). Operating temperatures above +150 °C require special heat treatment. Bearings treated in this way are available by agreement and are identified by the suffix S1, S2, S3 or S4 to DIN 623-1 ➤ Table.
Above S1, there is a reduction in hardness that must be taken into consideration in the rating life calculation.
Operating temperature and suffixes for dimensionally stabilised bearings
Maximum operating temperature |
Suffix for dimensionally stabilised bearings |
---|---|
°C |
|
+120 |
SN1) (suffix SN not stated) |
+150 |
S01) |
+150 |
S0B2) (suffix B not stated) |
+200 |
S11) |
+250 |
S21) |
+300 |
S31) |
+350 |
S41) |
- Inner ring and outer ring stabilised for stated operating temperature
- Inner ring stabilised up to +150 °C
Track rollers
Normal operating temperature = +70 °C
An operating temperature of +70 °C is regarded as a normal operating temperature. Further temperature data in the product descriptions must be observed.
Sealed bearings
Temperature limits
The permissible temperature for sealed bearings is dependent on the requirements for the operating life of the grease filling and on the action of the contact seals. Sealed bearings are greased with specially tested, high performance, high quality greases. These greases can withstand +120 °C for short periods. At or above continuous temperatures of +70 °C, a reduction in the operating life of standard greases with a lithium soap base must be expected.
Special greases are often required for high temperatures
In many cases, adequate operating life values are only achieved at high temperatures through the use of special greases. In these cases, it must also be checked whether seals made from especially heat-resistant materials must be used. The operating limit of normal contact seals is +100 °C.
If high temperature synthetic materials are used for seals and greases, it must be noted that the particularly high performance materials containing fluoride may give off harmful gases and vapours when heated to approx. +300 °C and above. This may occur, for example, if a welding torch is used in the dismantling of a bearing.
Observe safety data sheets at high temperatures
High temperatures are critical especially in the case of seals made from fluoro rubber (FKM, FPM, e. g. Viton®) or greases containing fluoride, such as the rolling bearing greases Arcanol TEMP200 and greases to GA11. If high temperatures are unavoidable, attention must be paid to the valid safety data sheet for the specific fluoride-containing material, which can be obtained upon request.
Dimensional and running tolerances
International standards are usually valid for the main dimensions and running accuracy of rolling bearings. Unless specified otherwise, the tolerances for radial rolling bearings correspond to ISO 492:2014 and, for axial rolling bearings, to ISO 199:2014. Information on which bearings are supplied with which tolerances is provided in the relevant product chapters.
Main dimensions
Main dimensions of bearings ➤ Figure.
Main dimensions of bearings |
![]() |
Accuracy (tolerance classes)
Tolerance class Normal
The dimensional and running accuracy of rolling bearings corresponds to tolerance class Normal. For bearings with increased accuracy, the tolerances are restricted to values in the classes 6, 5, 4 and 2. Tolerance tables for the individual tolerance classes ➤ Table to ➤ Table.
Super precision bearings
In addition to the standardised tolerance classes, super precision bearings are also produced to the tolerance classes P4S, SP and UP. These tolerances are listed in the relevant product descriptions.
Tolerance symbols, toleranced characteristics, deviations for radial and axial rolling bearings
The following restrictions apply to the stated specification modifiers in ➤ Table and ➤ Table:
- The specification modifier
is not indicated on a drawing if the two-point size is defined as the default specification
- The specification modifier
is not suitable for cases where there is no material with mating contact, for example the outer ring of a tapered roller bearing with significant edge rounding on the back face and small front face. Solutions must be developed within the framework of the GPS system and taken into consideration in the future
Symbols for nominal dimensions, characteristics and specification modifiers for radial rolling bearings in accordance with ISO 492:2014
Symbol for nominal dimension1)2) |
||||
---|---|---|---|---|
Tolerance symbol for characteristic2) |
GPS symbol and specification modifier |
Description for radial bearings |
Old term |
|
Symbols in accordance with ISO 1101 and ISO 14405-1 |
In accordance with ISO 492:2014 |
In accordance with ISO 1132-1:2000 |
||
Width |
||||
B |
‒ |
Nominal inner ring width |
Nominal inner ring width |
|
tΔBs |
![]() |
Symmetrical rings Deviation of a two-point size of inner ring width from its nominal size ΔBs = Bs – B |
Deviation of a single inner ring width |
|
tΔBs | ![]() |
Asymmetrical rings, upper limit Deviation of a minimum circumscribed size of inner ring width, between two opposite lines, in any longitudinal section which includes the inner ring bore axis, from its nominal size |
Deviation of a single inner ring width | |
tΔBs | ![]() |
Asymmetrical rings, lower limit Deviation of a two-point size of inner ring width from its nominal size |
Deviation of a single inner ring width | |
tVBs |
![]() |
Symmetrical rings Range of two-point sizes of inner ring width VBs = Bs max – Bs min |
Variation of inner ring width |
|
tVBs | ![]() |
Asymmetrical rings Range of minimum circumscribed sizes of inner ring width, between two opposite lines, obtained from any longitudinal section which includes the inner ring bore axis |
Variation of inner ring width | |
Symbol for nominal dimension1)2) |
||||
Tolerance symbol for characteristic2) |
GPS symbol and specification modifier |
Description for radial bearings |
Old term |
|
Width |
||||
C |
‒ |
Nominal outer ring width |
Nominal outer ring width |
|
tΔCs |
![]() |
Symmetrical rings Deviation of a two-point size of outer ring width from its nominal size ΔCs = Cs – C |
Deviation of a single outer ring width |
|
tΔCs | ![]() |
Asymmetrical rings, upper limit Deviation of a minimum circumscribed size of outer ring width, between two opposite lines, in any longitudinal section which includes the outer ring outside surface axis, from its nominal size |
Deviation of a single outer ring width | |
tΔCs | ![]() |
Asymmetrical rings, lower limit Deviation of a two-point size of outer ring width from its nominal size |
Deviation of a single outer ring width | |
tVCs |
![]() |
Symmetrical rings Range of two-point sizes of outer ring width VCs = Cs max – Cs min |
Variation of outer ring width |
|
tVCs | ![]() |
Asymmetrical rings Range of minimum circumscribed sizes of outer ring width, between two opposite lines, obtained from any longitudinal section which includes the outer ring outside surface axis |
Variation of outer ring width | |
C1 |
‒ |
Nominal outer ring flange width |
Nominal outer ring flange width |
|
tΔC1s |
![]() |
Deviation of a two-point size of outer ring flange width from its nominal size |
Deviation of a single outer ring flange width |
|
tVC1s |
![]() |
Range of two-point sizes of outer ring flange width VC1s = C1s max – C1s min |
Variation of outer ring flange width |
|
Symbol for nominal dimension1)2) |
||||
Tolerance symbol for characteristic2) |
GPS symbol and specification modifier |
Description for radial bearings |
Old term |
|
Diameter |
||||
d |
‒ |
Nominal bore diameter of a cylindrical bore or at the theoretical small end of a tapered bore |
Nominal bore diameter |
|
tΔds |
![]() |
Deviation of a two-point size of the bore diameter from its nominal size Δds = ds – d |
Deviation of a single bore diameter |
|
tVdsp |
![]() |
Range of two-point sizes of bore diameter in any cross-section of a cylindrical or tapered bore Vdsp = ds max – ds min |
Variation of single bore diameter in a single plane |
|
tΔdmp |
![]() |
Cylindrical bore Deviation of a mid-range size (out of two-point sizes) of bore diameter in any cross-section from its nominal size dmp = (d max + d min)/2 |
Deviation of mean bore diameter in a single plane |
|
tΔdmp | ![]() |
Tapered bore Deviation of a mid-range size (out of two-point sizes) of bore diameter at the theoretical small end of a tapered bore from its nominal size |
Deviation of mean bore diameter in a single plane | |
tVdmp |
![]() |
Range of mid-range sizes (out of two-point sizes) of bore diameter obtained from any cross-section of a cylindrical bore Vdmp = dmp max – dmp min |
Variation of mean bore diameter |
|
d1 |
‒ |
Nominal diameter at the theoretical large end of a tapered bore |
‒ |
|
tΔd1mp |
![]() |
Deviation of a mid-range size (out of two-point sizes) of bore diameter at the theoretical large end of a tapered bore from its nominal size |
‒ |
|
Symbol for nominal dimension1)2) |
||||
Tolerance symbol for characteristic2) |
GPS symbol and specification modifier |
Description for radial bearings |
Old term |
|
Diameter |
||||
D |
‒ |
Nominal outside diameter |
Nominal outside diameter |
|
tΔDs |
![]() |
Deviation of a two-point size of outside diameter from its nominal size |
Deviation of a single outside diameter |
|
tVDsp |
![]() |
Range of two-point sizes of outside diameter in any cross-section |
Variation of a single outside diameter in a single plane |
|
tΔDmp |
![]() |
Deviation of a mid-range size (out of two-point sizes) of outside diameter in any cross-section from its nominal size Dmp = (D max + D min)/2 |
Deviation of mean outside diameter in a single plane |
|
tVDmp |
![]() |
Range of mid-range sizes (out of two-point sizes) of outside diameter obtained from any cross-section VDmp = Dmp max – Dmp min |
Variation of mean outside diameter |
|
D1 |
‒ |
Nominal outside diameter of outer ring flange |
‒ |
|
tΔD1s |
![]() |
Deviation of a two-point size of outside diameter of outer ring flange from its nominal size |
‒ |
|
tKea |
![]() |
Circular radial run-out of outer ring outside surface of assembled bearing with respect to datum, i.e. axis, established from the inner ring bore surface |
Radial run-out of outer ring of assembled bearing |
|
tKia |
![]() |
Circular radial run-out of inner ring bore of assembled bearing with respect to datum, i.e. axis, established from the outer ring outside surface |
Radial run-out of inner ring of assembled bearing |
|
tSd |
![]() |
Circular axial run-out of inner ring face with respect to datum, i.e. axis, established from the inner ring bore surface |
Perpendicularity of inner ring face with respect to the bore |
|
tSD |
![]() |
Perpendicularity of outer ring outside surface axis with respect to datum established from the outer ring face |
Perpendicularity of outer ring outside surface with respect to the face |
|
tSD1 |
![]() |
Perpendicularity of outer ring outside surface axis with respect to datum established from the outer ring flange back face |
Perpendicularity of outer ring outside surface with respect to the flange back face |
|
tSea |
![]() |
Circular axial run-out of outer ring face of assembled bearing with respect to datum, i.e. axis, established from the inner ring bore surface |
Axial run-out of outer ring of assembled bearing |
|
tSea1 |
![]() |
Circular axial run-out of outer ring flange back face of assembled bearing with respect to datum, i.e. axis, established from the inner ring bore surface |
Axial run-out of outer ring flange back face of assembled bearing |
|
tSia |
![]() |
Circular axial run-out of inner ring face of assembled bearing with respect to datum, i.e. axis, established from the outer ring outside surface |
Axial run-out of inner ring of assembled bearing |
|
Symbol for nominal dimension1)2) |
||||
Tolerance symbol for characteristic2) |
GPS symbol and specification modifier |
Description for radial bearings |
Old term |
|
Tapered bore |
||||
SL |
‒ |
Taper slope: The difference between nominal diameters at the theoretical large end and small end of a tapered bore SL = d1 – d |
‒ |
|
tΔSL |
‒ |
Deviation of taper slope of a tapered inner ring bore from its nominal size (description based on DIN EN ISO 1119) ΔSL = Δd1mp – Δdmp |
‒ |
|
α |
‒ |
Frustum angle of tapered inner ring bore |
‒ |
|
Symbol for nominal dimension1)2) |
||||
Tolerance symbol for characteristic2) |
GPS symbol and specification modifier |
Description for radial bearings |
Old term |
|
Width of assembled bearing |
||||
T |
‒ |
Nominal assembled bearing width |
Nominal bearing width |
|
tΔTs |
![]() |
Deviation of minimum circumscribed size of assembled bearing width from its nominal size |
Deviation of the actual bearing width |
|
T1 |
‒ |
Nominal effective width of inner subunit assembled with a master outer ring |
Nominal effective width of inner subunit |
|
tΔT1s |
![]() |
Deviation of minimum circumscribed size of effective width (inner subunit assembled with a master outer ring) from its nominal size |
Deviation of the actual effective width of inner subunit |
|
T2 |
‒ |
Nominal effective width of outer ring assembled with a master inner subunit |
Nominal effective width of outer ring |
|
tΔT2s |
![]() |
Deviation of minimum circumscribed size of effective width (outer ring assembled with a master inner subunit) from its nominal size |
Deviation of the actual effective width of outer ring |
|
TF |
‒ |
Nominal assembled flanged bearing width |
‒ |
|
tΔTFs |
![]() |
Deviation of minimum circumscribed size of assembled flange bearing width from its nominal size |
‒ |
|
TF2 |
‒ |
Nominal effective width of flanged outer ring assembled with a master inner subunit |
‒ |
|
tΔTF2s |
![]() |
Deviation of minimum circumscribed size of effective width (flanged outer ring assembled with a master inner subunit) from its nominal size |
‒ |
- Symbols for the nominal dimension are printed in bold; they indicate size dimensions and spacings.
- Symbols in accordance with ISO 1101 and ISO 14405-1.
- Specification modifiers for the direction of action of the mass in accordance with ISO/TS 17863.
- Valid only for axial ball bearings and axial cylindrical roller bearings with a 90° contact angle.
Symbols for nominal dimensions, characteristics and specification modifiers for axial rolling bearings in accordance with ISO 199:2014
Symbol for nominal dimension1)2) Tolerance symbol for characteristic2) |
GPS symbol and specification modifier |
Description for axial bearings |
Old term |
|
---|---|---|---|---|
Symbols in accordance with ISO 1101 and ISO 14405-1 |
In accordance with ISO 199:2014 |
In accordance with ISO 1132-1:2000 |
||
Diameter |
||||
d |
‒ |
Nominal bore diameter of shaft washer, single-direction bearing |
Nominal bore diameter of shaft washer |
|
tΔdmp |
![]() |
Deviation of a mid-range size (out of two-point sizes) of shaft washer bore diameter in any cross-section from its nominal size dmp = (d max + d min)/2 |
Deviation of mean bore diameter in a single plane |
|
tVdsp |
![]() |
Range of two-point sizes of shaft washer bore diameter in any cross‑section Vdsp = ds max – ds min |
Variation of single bore diameter in a single plane |
|
d2 |
‒ |
Nominal bore diameter of central shaft washer, double-direction bearing |
‒ |
|
tΔd2mp |
![]() |
Deviation of a mid-range size (out of two-point sizes) of central shaft washer bore diameter in any cross-section from its nominal size d2mp = (d2 max + d2 min)/2 |
‒ |
|
tVd2sp |
![]() |
Range of two-point sizes of central shaft washer bore diameter in any cross-section |
Variation of single bore diameter in a single plane |
|
D |
‒ |
Nominal outside diameter of housing washer |
Nominal outside diameter of bore (housing washer) |
|
tΔDmp |
![]() |
Deviation of a mid-range size (out of two-point sizes) of housing washer outside diameter in any cross-section from its nominal size Dmp = (D max + D min)/2 |
Deviation of mean outside diameter in a single plane |
|
tVDsp |
![]() |
Range of two-point sizes of housing washer outside diameter in any cross-section VDsp = Ds max – Ds min |
Variation of a single outside diameter in a single plane |
|
Height |
||||
T |
‒ |
Nominal assembled bearing height, single-direction bearing |
Nominal bearing height |
|
tΔTs |
![]() |
Deviation of minimum circumscribed size of assembled bearing height from its nominal size, single-direction bearing |
Deviation of the actual bearing height |
|
T1 |
‒ |
Nominal assembled bearing height, double-direction bearing |
‒ |
|
tΔT1s |
![]() |
Deviation of minimum circumscribed size of assembled bearing height from its nominal size, double-direction bearing |
‒ |
|
tSe4) |
![]() |
Axial cylindrical roller bearings Range of two-point sizes of thickness between housing washer raceway and the back face |
Variation in thickness between housing washer raceway and back face |
|
tSe4) | ![]() |
Axial ball bearings Range of minimum spherical sizes between the raceway and the opposite back face of the housing washer, obtained from any longitudinal section which includes the housing washer outside surface axis |
Variation in thickness between housing washer raceway and back face | |
tSi4) |
![]() |
Axial cylindrical roller bearings Range of two-point sizes of thickness between shaft washer raceway and the back face |
Variation in thickness between shaft washer raceway and back face |
|
tSi4) | ![]() |
Axial ball bearings Range of minimum spherical sizes between the raceway and the opposite back face of the shaft washer, obtained from any longitudinal section which includes the shaft washer bore axis |
Variation in thickness between housing washer raceway and back face | |
continued ▲ |
- Symbols for the nominal dimension are printed in bold; they indicate size dimensions and spacings.
- Symbols in accordance with ISO 1101 and ISO 14405-1.
- Specification modifiers for the direction of action of the mass in accordance with ISO/TS 17863.
- Valid only for axial ball bearings and axial cylindrical roller bearings with a 90° contact angle.
Radial bearings, excluding tapered roller bearings
Tolerance class Normal, inner ring
Nominal |
Bore deviation |
Variation |
Radial runout |
|||||
---|---|---|---|---|---|---|---|---|
d |
tΔdmp |
tVdsp |
tVdmp |
tKia |
||||
μm |
||||||||
max. |
||||||||
mm |
μm |
Diameter series |
μm |
μm |
||||
over |
incl. |
U |
L |
9 |
0, 1 |
2, 3, 4 |
max. |
max. |
‒ |
2,5 |
0 |
–8 |
10 |
8 |
6 |
6 |
10 |
2,5 |
10 |
0 |
–8 |
10 |
8 |
6 |
6 |
10 |
10 |
18 |
0 |
–8 |
10 |
8 |
6 |
6 |
10 |
18 |
30 |
0 |
–10 |
13 |
10 |
8 |
8 |
13 |
30 |
50 |
0 |
–12 |
15 |
12 |
9 |
9 |
15 |
50 |
80 |
0 |
–15 |
19 |
19 |
11 |
11 |
20 |
80 |
120 |
0 |
–20 |
25 |
25 |
15 |
15 |
25 |
120 |
180 |
0 |
–25 |
31 |
31 |
19 |
19 |
30 |
180 |
250 |
0 |
–30 |
38 |
38 |
23 |
23 |
40 |
250 |
315 |
0 |
–35 |
44 |
44 |
26 |
26 |
50 |
315 |
400 |
0 |
–40 |
50 |
50 |
30 |
30 |
60 |
400 |
500 |
0 |
–45 |
56 |
56 |
34 |
34 |
65 |
500 |
630 |
0 |
–50 |
63 |
63 |
38 |
38 |
70 |
630 |
800 |
0 |
–75 |
‒ |
‒ |
‒ |
‒ |
80 |
800 |
1 000 |
0 |
–100 |
‒ |
‒ |
‒ |
‒ |
90 |
1000 |
1 250 |
0 |
–125 |
‒ |
‒ |
‒ |
‒ |
100 |
1250 |
1 600 |
0 |
–160 |
‒ |
‒ |
‒ |
‒ |
120 |
1600 |
2 000 |
0 |
–200 |
‒ |
‒ |
‒ |
‒ |
140 |
Tolerance symbols in accordance with ISO 492 ➤ Table
U = upper limit deviation
L = lower limit deviation
Tolerance class Normal, inner ring width tolerances
Nominal |
Deviation |
Variation |
|||
---|---|---|---|---|---|
d |
tΔBs |
tVBs |
|||
μm |
|||||
mm |
All |
Normal |
Modified1) |
μm |
|
over |
incl. |
U |
L |
L |
max. |
‒ |
2,5 |
0 |
–40 |
‒ |
12 |
2,5 |
10 |
0 |
–120 |
–250 |
15 |
10 |
18 |
0 |
–120 |
–250 |
20 |
18 |
30 |
0 |
–120 |
–250 |
20 |
30 |
50 |
0 |
–120 |
–250 |
20 |
50 |
80 |
0 |
–150 |
–380 |
25 |
80 |
120 |
0 |
–200 |
–380 |
25 |
120 |
180 |
0 |
–250 |
–500 |
30 |
180 |
250 |
0 |
–300 |
–500 |
30 |
250 |
315 |
0 |
–350 |
–500 |
35 |
315 |
400 |
0 |
–400 |
–630 |
40 |
400 |
500 |
0 |
–450 |
‒ |
50 |
500 |
630 |
0 |
–500 |
‒ |
60 |
630 |
800 |
0 |
–750 |
‒ |
70 |
800 |
1 000 |
0 |
–1 000 |
‒ |
80 |
1 000 |
1 250 |
0 |
–1 250 |
‒ |
100 |
1 250 |
1 600 |
0 |
–1 600 |
‒ |
120 |
1 600 |
2 000 |
0 |
–2 000 |
‒ |
140 |
Tolerance symbols in accordance with ISO 492 ➤ Table
U = upper limit deviation
L = lower limit deviation
- Only for bearings manufactured specifically for use as matched pairs, with the exception of deep groove ball bearings.
Tolerance class Normal, outer ring1)
Nominal size |
Deviation of |
Variation |
Radial |
||||||
---|---|---|---|---|---|---|---|---|---|
D |
tΔDmp |
tVDsp |
tVDmp2) |
tKea |
|||||
μm |
|||||||||
max. |
|||||||||
Open |
Bearings |
||||||||
mm |
μm |
Diameter series |
μm |
μm |
|||||
over |
incl. |
U |
L |
9 |
0, 1 |
2, 3, 4 |
max. |
max. |
|
‒ |
6 |
0 |
–8 |
10 |
8 |
6 |
10 |
6 |
15 |
6 |
18 |
0 |
–8 |
10 |
8 |
6 |
10 |
6 |
15 |
18 |
30 |
0 |
–9 |
12 |
9 |
7 |
12 |
7 |
15 |
30 |
50 |
0 |
–11 |
14 |
11 |
8 |
16 |
8 |
20 |
50 |
80 |
0 |
–13 |
16 |
13 |
10 |
20 |
10 |
25 |
80 |
120 |
0 |
–15 |
19 |
19 |
11 |
26 |
11 |
35 |
120 |
150 |
0 |
–18 |
23 |
23 |
14 |
30 |
14 |
40 |
150 |
180 |
0 |
–25 |
31 |
31 |
19 |
38 |
19 |
45 |
180 |
250 |
0 |
–30 |
38 |
38 |
23 |
‒ |
23 |
50 |
250 |
315 |
0 |
–35 |
44 |
44 |
26 |
‒ |
26 |
60 |
315 |
400 |
0 |
–40 |
50 |
50 |
30 |
‒ |
30 |
70 |
400 |
500 |
0 |
–45 |
56 |
56 |
34 |
‒ |
34 |
80 |
500 |
630 |
0 |
–50 |
63 |
63 |
38 |
‒ |
38 |
100 |
630 |
800 |
0 |
–75 |
94 |
94 |
55 |
‒ |
55 |
120 |
800 |
1 000 |
0 |
–100 |
125 |
125 |
75 |
‒ |
75 |
140 |
1 000 |
1 250 |
0 |
–125 |
‒ |
‒ |
‒ |
‒ |
‒ |
160 |
1 250 |
1 600 |
0 |
–160 |
‒ |
‒ |
‒ |
‒ |
‒ |
190 |
1 600 |
2 000 |
0 |
–200 |
‒ |
‒ |
‒ |
‒ |
‒ |
220 |
2 000 |
2 500 |
0 |
–250 |
‒ |
‒ |
‒ |
‒ |
‒ |
250 |
Tolerance symbols in accordance with ISO 492 ➤ Table
U = upper limit deviation
L = lower limit deviation
- tΔCs, tΔC1s, tVCs and tVC1s are identical to tΔBs and tVBs for the inner ring of the corresponding bearing ➤ Table.
- Applies before assembly of the bearing and after removal of internal and/or external snap rings.
Radial bearings, excluding tapered roller bearings
Tolerance class 6, inner ring
Nominal |
Bore |
Variation |
Radial |
|||||
---|---|---|---|---|---|---|---|---|
d |
tΔdmp |
tVdsp |
tVdmp |
tKia |
||||
μm |
||||||||
max. |
||||||||
mm |
μm |
Diameter |
μm |
μm |
||||
over |
incl. |
U |
L |
9 |
0, 1 |
2, 3, 4 |
max. |
max. |
‒ |
2,5 | 0 | –7 | 9 | 7 | 5 | 5 | 5 |
2,5 | 10 | 0 | –7 | 9 | 7 | 5 | 5 | 6 |
10 | 18 | 0 | –7 | 9 | 7 | 5 | 5 | 7 |
18 | 30 | 0 | –8 | 10 | 8 | 6 | 6 | 8 |
30 | 50 | 0 | –10 | 13 | 10 | 8 | 8 | 10 |
50 | 80 | 0 | –12 | 15 | 15 | 9 | 9 | 10 |
80 | 120 | 0 | –15 | 19 | 19 | 11 | 11 | 13 |
120 | 180 | 0 | –18 | 23 | 23 | 14 | 14 | 18 |
180 | 250 | 0 | –22 | 28 | 28 | 17 | 17 | 20 |
250 | 315 | 0 | –25 | 31 | 31 | 19 | 19 | 25 |
315 | 400 | 0 | –30 | 38 | 38 | 23 | 23 | 30 |
400 | 500 | 0 | –35 | 44 | 44 | 26 | 26 | 35 |
500 | 630 | 0 | –40 | 50 | 50 | 30 | 30 | 40 |
Tolerance symbols in accordance with ISO 492 ➤ Table
U = upper limit deviation
L = lower limit deviation
Tolerance class 6, inner ring width tolerances
Nominal |
Deviation of |
Variation of |
|||
---|---|---|---|---|---|
d |
tΔBs |
tVBs |
|||
μm |
|||||
mm |
All |
Normal |
Modified1) |
μm |
|
over |
incl. |
U |
L |
L |
max. |
‒ |
2,5 | 0 | –40 |
‒ |
12 |
2,5 | 10 | 0 | –120 | –250 | 15 |
10 | 18 | 0 | –120 | –250 | 20 |
18 | 30 | 0 | –120 | –250 | 20 |
30 | 50 | 0 | –120 | –250 | 20 |
50 | 80 | 0 | –150 | –380 | 25 |
80 | 120 | 0 | –200 | –380 | 25 |
120 | 180 | 0 | –250 | –550 | 30 |
180 | 250 | 0 | –300 | –500 | 30 |
250 | 315 | 0 | –350 | –500 | 35 |
315 | 400 | 0 | –400 | –630 | 40 |
400 | 500 | 0 | –450 |
‒ |
45 |
500 | 630 | 0 | –500 |
‒ |
50 |
Tolerance symbols in accordance with ISO 492 ➤ Table
U = upper limit deviation
L = lower limit deviation
- Only for bearings manufactured specifically for use as matched pairs, with the exception of deep groove ball bearings.
Tolerance class 6, outer ring1)
Nominal size |
Deviation |
Variation |
Radial |
||||||
---|---|---|---|---|---|---|---|---|---|
D |
tΔDmp |
tVDsp |
tVDmp2) |
tKea |
|||||
μm |
|||||||||
max. |
|||||||||
Open bearings |
Bearings |
||||||||
mm |
μm |
Diameter series |
μm |
μm |
|||||
over |
incl. |
U |
L |
9 |
0, 1 |
2, 3, 4 |
max. |
max. |
|
‒ |
6 | 0 | –7 | 9 | 7 | 5 | 9 | 5 | 8 |
6 | 18 | 0 | –7 | 9 | 7 | 5 | 9 | 5 | 8 |
18 | 30 | 0 | –8 | 10 | 8 | 6 | 10 | 6 | 9 |
30 | 50 | 0 | –9 | 11 | 9 | 7 | 13 | 7 | 10 |
50 | 80 | 0 | –11 | 14 | 11 | 8 | 16 | 8 | 13 |
80 | 120 | 0 | –13 | 16 | 16 | 10 | 20 | 10 | 18 |
120 | 150 | 0 | –15 | 19 | 19 | 11 | 25 | 11 | 20 |
150 | 180 | 0 | –18 | 23 | 23 | 14 | 30 | 14 | 23 |
180 | 250 | 0 | –20 | 25 | 25 | 15 |
‒ |
15 | 25 |
250 | 315 | 0 | –25 | 31 | 31 | 19 |
‒ |
19 | 30 |
315 | 400 | 0 | –28 | 35 | 35 | 21 |
‒ |
21 | 35 |
400 | 500 | 0 | –33 | 41 | 41 | 25 |
‒ |
25 | 40 |
500 | 630 | 0 | –38 | 48 | 48 | 29 |
‒ |
29 | 50 |
630 | 800 | 0 | –45 | 56 | 56 | 34 |
‒ |
34 | 60 |
800 | 1000 | 0 | –60 | 75 | 75 | 45 |
‒ |
45 | 75 |
Tolerance symbols in accordance with ISO 492 ➤ Table
U = upper limit deviation
L = lower limit deviation
- tΔCs, tΔC1s, tVCs and tVC1s are identical to tΔBs and tVBs for the inner ring of the corresponding bearing ➤ Table
- Applies before assembly of the bearing and after removal of internal and/or external snap rings.
Radial bearings, excluding tapered roller bearings
Tolerance class 5, inner ring
Nominal |
Bore |
Variation |
Radial |
Axial |
||||
---|---|---|---|---|---|---|---|---|
d |
tΔdmp |
tVdsp |
tVdmp |
tKia |
tSd |
|||
μm |
||||||||
max. |
||||||||
mm |
μm |
Diameter |
μm |
μm |
μm |
|||
over |
incl. |
U |
L |
9 |
0, 1, 2, 3, 4 |
max. |
max. |
max. |
‒ |
2,5 |
0 |
–5 |
5 |
4 |
3 |
4 |
7 |
2,5 |
10 |
0 |
–5 |
5 |
4 |
3 |
4 |
7 |
10 |
18 |
0 |
–5 |
5 |
4 |
3 |
4 |
7 |
18 |
30 |
0 |
–6 |
6 |
5 |
3 |
4 |
8 |
30 |
50 |
0 |
–8 |
8 |
6 |
4 |
5 |
8 |
50 |
80 |
0 |
–9 |
9 |
7 |
5 |
5 |
8 |
80 |
120 |
0 |
–10 |
10 |
8 |
5 |
6 |
9 |
120 |
180 |
0 |
–13 |
13 |
10 |
7 |
8 |
10 |
180 |
250 |
0 |
–15 |
15 |
12 |
8 |
10 |
11 |
250 |
315 |
0 |
–18 |
18 |
14 |
9 |
13 |
13 |
315 |
400 |
0 |
–23 |
23 |
18 |
12 |
15 |
15 |
Tolerance symbols in accordance with ISO 492 ➤ Table
U = upper limit deviation
L = lower limit deviation
Tolerance class 5, width tolerances, inner ring
Nominal |
Deviation of |
Variation of |
Axial runout of |
|||
---|---|---|---|---|---|---|
d |
tΔBs |
tVBs |
tSia1) |
|||
μm |
||||||
mm |
All |
Normal |
Modified2) |
μm |
μm |
|
over |
incl. |
U |
L |
L |
max. |
max. |
‒ |
2,5 |
0 |
–40 |
–250 |
5 |
7 |
2,5 |
10 |
0 |
–40 |
–250 |
5 |
7 |
10 |
18 |
0 |
–80 |
–250 |
5 |
7 |
18 |
30 |
0 |
–120 |
–250 |
5 |
8 |
30 |
50 |
0 |
–120 |
–250 |
5 |
8 |
50 |
80 |
0 |
–150 |
–250 |
6 |
8 |
80 |
120 |
0 |
–200 |
–380 |
7 |
9 |
120 |
180 |
0 |
–250 |
–380 |
8 |
10 |
180 |
250 |
0 |
–300 |
–500 |
10 |
13 |
250 |
315 |
0 |
–350 |
–500 |
13 |
15 |
315 |
400 |
0 |
–400 |
–630 |
15 |
20 |
Tolerance symbols in accordance with ISO 492 ➤ Table
U = upper limit deviation
L = lower limit deviation
- Only for deep groove and angular contact ball bearings.
- Only for bearings manufactured specifically for use as matched pairs, with the exception of deep groove ball bearings.
Tolerance class 5, outer ring1)
Nominal size of outside diameter |
Deviation |
Variation |
Radial runout |
Perpendicularity |
Axial runout |
|||||
---|---|---|---|---|---|---|---|---|---|---|
D |
tΔDmp |
tVDsp2) |
tVDmp3) |
tVCs |
tKea |
tSD |
tSea4) |
|||
μm |
||||||||||
max. |
||||||||||
mm |
μm |
Diameter series |
μm |
μm |
μm |
μm |
μm |
|||
over |
incl. |
U |
L |
9 |
0, 1, 2, 3, 4 |
max. |
max. |
max. |
max. |
max. |
‒ |
6 |
0 |
–5 |
5 |
4 |
3 |
5 |
5 |
4 |
8 |
6 |
18 |
0 |
–5 |
5 |
4 |
3 |
5 |
5 |
4 |
8 |
18 |
30 |
0 |
–6 |
6 |
5 |
3 |
5 |
6 |
4 |
8 |
30 |
50 |
0 |
–7 |
7 |
5 |
4 |
5 |
7 |
4 |
8 |
50 |
80 |
0 |
–9 |
9 |
7 |
5 |
6 |
8 |
4 |
10 |
80 |
120 |
0 |
–10 |
10 |
8 |
5 |
8 |
10 |
4,5 |
11 |
120 |
150 |
0 |
–11 |
11 |
8 |
6 |
8 |
11 |
5 |
13 |
150 |
180 |
0 |
–13 |
13 |
10 |
7 |
8 |
13 |
5 |
14 |
180 |
250 |
0 |
–15 |
15 |
11 |
8 |
10 |
15 |
5,5 |
15 |
250 |
315 |
0 |
–18 |
18 |
14 |
9 |
11 |
18 |
6,5 |
18 |
315 |
400 |
0 |
–20 |
20 |
15 |
10 |
13 |
20 |
6,5 |
20 |
400 |
500 |
0 |
–23 |
23 |
17 |
12 |
15 |
23 |
7,5 |
23 |
500 |
630 |
0 |
–28 |
28 |
21 |
14 |
18 |
25 |
9 |
25 |
630 |
800 |
0 |
–35 |
35 |
26 |
18 |
20 |
30 |
10 |
30 |
Tolerance symbols in accordance with ISO 492 ➤ Table
U = upper limit deviation
L = lower limit deviation
- tΔCs is identical to tΔBs for the inner ring of the corresponding bearing ➤ Table.
- No values are given for radial ball bearings with sealing shields or sealing washers.
- Applies before assembly of the bearing and after removal of internal and/or external snap rings.
- Only for deep groove and angular contact ball bearings.
Radial bearings, excluding tapered roller bearings
Tolerance class 4, inner ring
Nominal |
Bore deviation |
Deviation of a single bore diameter |
Variation |
Radial runout |
|||||
---|---|---|---|---|---|---|---|---|---|
d |
tΔdmp |
tΔds |
tVdsp |
tVdmp |
tKia |
||||
μm |
μm |
μm |
|||||||
Diameter series |
|||||||||
mm |
9 |
0, 1, 2, 3, 4 |
9 |
0, 1, 2, 3, 4 |
μm |
μm |
|||
over |
incl. |
U |
L |
U |
L |
max. |
max. |
max. |
max. |
‒ |
2,5 |
0 |
–4 |
0 |
–4 |
4 |
3 |
2 |
2,5 |
2,5 |
10 |
0 |
–4 |
0 |
–4 |
4 |
3 |
2 |
2,5 |
10 |
18 |
0 |
–4 |
0 |
–4 |
4 |
3 |
2 |
2,5 |
18 |
30 |
0 |
–5 |
0 |
–5 |
5 |
4 |
2,5 |
3 |
30 |
50 |
0 |
–6 |
0 |
–6 |
6 |
5 |
3 |
4 |
50 |
80 |
0 |
–7 |
0 |
–7 |
7 |
5 |
3,5 |
4 |
80 |
120 |
0 |
–8 |
0 |
–8 |
8 |
6 |
4 |
5 |
120 |
180 |
0 |
–10 |
0 |
–10 |
10 |
8 |
5 |
6 |
180 |
250 |
0 |
–12 |
0 |
–12 |
12 |
9 |
6 |
8 |
Tolerance symbols in accordance with ISO 492 ➤ Table
U = upper limit deviation
L = lower limit deviation
Tolerance class 4, width tolerances, inner ring
Nominal |
Deviation |
Variation |
Axial runout |
||||
---|---|---|---|---|---|---|---|
d |
tΔBs |
tVBs |
tSia1) |
tSd |
|||
μm |
|||||||
mm |
All |
Normal |
Modified2) |
μm |
μm |
μm |
|
over |
incl. |
U |
L |
L |
max. |
max. |
max. |
‒ |
2,5 |
0 |
–40 |
–250 |
2,5 |
3 |
3 |
2,5 |
10 |
0 |
–40 |
–250 |
2,5 |
3 |
3 |
10 |
18 |
0 |
–80 |
–250 |
2,5 |
3 |
3 |
18 |
30 |
0 |
–120 |
–250 |
2,5 |
4 |
4 |
30 |
50 |
0 |
–120 |
–250 |
3 |
4 |
4 |
50 |
80 |
0 |
–150 |
–250 |
4 |
5 |
5 |
80 |
120 |
0 |
–200 |
–380 |
4 |
5 |
5 |
120 |
180 |
0 |
–250 |
–380 |
5 |
7 |
6 |
180 |
250 |
0 |
–300 |
–500 |
6 |
8 |
7 |
Tolerance symbols in accordance with ISO 492 ➤ Table
U = upper limit deviation
L = lower limit deviation
- Only for deep groove and angular contact ball bearings.
- Only for bearings manufactured specifically for use as matched pairs, with the exception of deep groove ball bearings.
Tolerance class 4, outer ring
Nominal size of |
Deviation |
Deviation of a single outside diameter |
Variation |
Radial runout |
|||||
---|---|---|---|---|---|---|---|---|---|
D |
tΔDmp |
tΔDs |
tVDsp1) |
tVDmp |
tKea |
||||
μm |
μm |
μm |
|||||||
max. |
|||||||||
Diameter series |
|||||||||
mm |
9 |
0, 1, 2, 3, 4 |
9 |
0, 1, 2, 3, 4 |
μm |
μm |
|||
over |
incl. |
U |
L |
U |
L |
max. |
max. |
||
‒ |
6 |
0 |
–4 |
0 |
–4 |
4 |
3 |
2 |
3 |
6 |
18 |
0 |
–4 |
0 |
–4 |
4 |
3 |
2 |
3 |
18 |
30 |
0 |
–5 |
0 |
–5 |
5 |
4 |
2,5 |
4 |
30 |
50 |
0 |
–6 |
0 |
–6 |
6 |
5 |
3 |
5 |
50 |
80 |
0 |
–7 |
0 |
–7 |
7 |
5 |
3,5 |
5 |
80 |
120 |
0 |
–8 |
0 |
–8 |
8 |
6 |
4 |
6 |
120 |
150 |
0 |
–9 |
0 |
–9 |
9 |
7 |
5 |
7 |
150 |
180 |
0 |
–10 |
0 |
–10 |
10 |
8 |
5 |
8 |
180 |
250 |
0 |
–11 |
0 |
–11 |
11 |
8 |
6 |
10 |
250 |
315 |
0 |
–13 |
0 |
–13 |
13 |
10 |
7 |
11 |
315 |
400 |
0 |
–15 |
0 |
–15 |
15 |
11 |
8 |
13 |
continued ▼ |
Tolerance symbols in accordance with ISO 492 ➤ Table
U = upper limit deviation
L = lower limit deviation
- No values are given for bearings with sealing shields or sealing washers.
Tolerance class 4, outer ring
Nominal size of |
Perpendicularity |
Axial runout |
Deviation of a single outer ring width |
Variation |
|
---|---|---|---|---|---|
D |
tSD tSD1 |
tSea1) |
tΔCs |
tVCs |
|
mm |
μm |
μm |
μm |
μm |
|
over |
incl. |
max. |
max. |
max. |
|
‒ |
6 |
2 |
5 |
tΔCs is identical to tΔBs |
2,5 |
6 |
18 |
2 |
5 |
2,5 |
|
18 |
30 |
2 |
5 |
2,5 |
|
30 |
50 |
2 |
5 |
2,5 |
|
50 |
80 |
2 |
5 |
3 |
|
80 |
120 |
2,5 |
6 |
4 |
|
120 |
150 |
2,5 |
7 |
5 |
|
150 |
180 |
2,5 |
8 |
5 |
|
180 |
250 |
3,5 |
10 |
7 |
|
250 |
315 |
4 |
10 |
7 |
|
315 |
400 |
5 |
13 |
8 |
|
continued ▲ |
- Only for deep groove and angular contact ball bearings.
Radial bearings, excluding tapered roller bearings
Tolerance class 2, inner ring
Nominal |
Bore deviation |
Deviation of a single bore diameter |
Variation |
Radial runout |
||||
---|---|---|---|---|---|---|---|---|
d |
tΔdmp |
tΔds |
tVdsp |
tVdmp |
tKia |
|||
μm |
μm |
|||||||
Diameter series |
||||||||
mm |
9 |
0, 1, 2, 3, 4 |
μm |
μm |
μm |
|||
over |
incl. |
U |
L |
U |
L |
max. |
max. |
max. |
‒ |
2,5 |
0 |
–2,5 |
0 |
–2,5 |
2,5 |
1,5 |
1,5 |
2,5 |
10 |
0 |
–2,5 |
0 |
–2,5 |
2,5 |
1,5 |
1,5 |
10 |
18 |
0 |
–2,5 |
0 |
–2,5 |
2,5 |
1,5 |
1,5 |
18 |
30 |
0 |
–2,5 |
0 |
–2,5 |
2,5 |
1,5 |
2,5 |
30 |
50 |
0 |
–2,5 |
0 |
–2,5 |
2,5 |
1,5 |
2,5 |
50 |
80 |
0 |
–4 |
0 |
–4 |
4 |
2 |
2,5 |
80 |
120 |
0 |
–5 |
0 |
–5 |
5 |
2,5 |
2,5 |
120 |
150 |
0 |
–7 |
0 |
–7 |
7 |
3,5 |
2,5 |
150 |
180 |
0 |
–7 |
0 |
–7 |
7 |
3,5 |
5 |
180 |
250 |
0 |
–8 |
0 |
–8 |
8 |
4 |
5 |
Tolerance symbols in accordance with ISO 492 ➤ Table
U = upper limit deviation
L = lower limit deviation
Tolerance class 2, width tolerances, inner ring
Nominal |
Deviation |
Axial runout |
Variation |
||||
---|---|---|---|---|---|---|---|
d |
tΔBs |
tSd |
tSia1) |
tVBs |
|||
μm |
|||||||
mm |
All |
Normal |
Modified2) |
μm |
μm |
μm |
|
over |
incl. |
U |
L |
L |
max. |
max. |
max. |
‒ |
2,5 |
0 |
–40 |
–250 |
1,5 |
1,5 |
1,5 |
2,5 |
10 |
0 |
–40 |
–250 |
1,5 |
1,5 |
1,5 |
10 |
18 |
0 |
–80 |
–250 |
1,5 |
1,5 |
1,5 |
18 |
30 |
0 |
–120 |
–250 |
1,5 |
2,5 |
1,5 |
30 |
50 |
0 |
–120 |
–250 |
1,5 |
2,5 |
1,5 |
50 |
80 |
0 |
–150 |
–250 |
1,5 |
2,5 |
1,5 |
80 |
120 |
0 |
–200 |
–380 |
2,5 |
2,5 |
2,5 |
120 |
150 |
0 |
–250 |
–380 |
2,5 |
2,5 |
2,5 |
150 |
180 |
0 |
–250 |
–380 |
4 |
5 |
4 |
180 |
250 |
0 |
–300 |
–500 |
5 |
5 |
5 |
Tolerance symbols in accordance with ISO 492 ➤ Table
U = upper limit deviation
L = lower limit deviation
- Only for deep groove and angular contact ball bearings.
- Only for bearings manufactured specifically for use as matched pairs, with the exception of deep groove ball bearings.
Nominal |
Deviation of outside diameter |
Variation |
Radial runout |
|||||
---|---|---|---|---|---|---|---|---|
D |
tΔDmp |
tΔDs |
tVDsp1) |
tVDmp |
tKea |
|||
μm |
μm |
|||||||
Diameter series |
||||||||
mm |
9 |
0, 1, 2, 3, 4 |
μm |
μm |
μm |
|||
over |
incl. |
U |
L |
U |
L |
max. |
max. |
max. |
‒ |
6 |
0 |
–2,5 |
0 |
–2,5 |
2,5 |
1,5 |
1,5 |
6 |
18 |
0 |
–2,5 |
0 |
–2,5 |
2,5 |
1,5 |
1,5 |
18 |
30 |
0 |
–4 |
0 |
–4 |
4 |
2 |
2,5 |
30 |
50 |
0 |
–4 |
0 |
–4 |
4 |
2 |
2,5 |
50 |
80 |
0 |
–4 |
0 |
–4 |
4 |
2 |
4 |
80 |
120 |
0 |
–5 |
0 |
–5 |
5 |
2,5 |
5 |
120 |
150 |
0 |
–5 |
0 |
–5 |
5 |
2,5 |
5 |
150 |
180 |
0 |
–7 |
0 |
–7 |
7 |
3,5 |
5 |
180 |
250 |
0 |
–8 |
0 |
–8 |
8 |
4 |
7 |
250 |
315 |
0 |
–8 |
0 |
–8 |
8 |
4 |
7 |
315 |
400 |
0 |
–10 |
0 |
–10 |
10 |
5 |
8 |
continued ▼ |
Tolerance symbols in accordance with ISO 492 ➤ Table
U = upper limit deviation
L = lower limit deviation
- No values are given for bearings with sealing shields or sealing washers.
Tolerance class 2, outer ring
Nominal |
Perpendicularity |
Axial runout |
Deviation |
Variation |
|
---|---|---|---|---|---|
D |
tSD tSD1 |
tSea1) |
tΔCs |
tVCs |
|
mm |
μm |
μm |
μm |
μm |
|
over |
incl. |
max. |
max. |
max. |
max. |
‒ |
6 |
0,75 |
1,5 |
tΔCs is identical to tΔBs |
1,5 |
6 |
18 |
0,75 |
1,5 |
1,5 |
|
18 |
30 |
0,75 |
2,5 |
1,5 |
|
30 |
50 |
0,75 |
2,5 |
1,5 |
|
50 |
80 |
0,75 |
4 |
1,5 |
|
80 |
120 |
1,25 |
5 |
2,5 |
|
120 |
150 |
1,25 |
5 |
2,5 |
|
150 |
180 |
1,25 |
5 |
2,5 |
|
180 |
250 |
2 |
7 |
4 |
|
250 |
315 |
2,5 |
7 |
5 |
|
315 |
400 |
3,5 |
8 |
7 |
|
continued ▲ |
Tolerance symbols in accordance with ISO 492 ➤ Table
U = upper limit deviation
L = lower limit deviation
- Only for deep groove and angular contact ball bearings.
Bearings with tapered bore
Tolerances for tapered bores in accordance with ISO 492, taper 1:12, tolerance class Normal
Nominal bore diameter |
Bore deviation |
Variation |
Deviation of taper slope |
|||
---|---|---|---|---|---|---|
d |
tΔdmp |
tVdsp1) |
tΔSL |
|||
mm |
μm |
μm |
μm |
|||
over |
incl. |
U |
L |
max. |
U |
L |
18 | 30 | +33 | 0 | 13 | +21 | 0 |
30 | 50 | +39 | 0 | 16 | +25 | 0 |
50 | 80 | +46 | 0 | 19 | +30 | 0 |
80 | 120 | +54 | 0 | 22 | +35 | 0 |
120 | 180 | +63 | 0 | 40 | +40 | 0 |
180 | 250 | +72 | 0 | 46 | +46 | 0 |
250 | 315 | +81 | 0 | 52 | +52 | 0 |
315 | 400 | +89 | 0 | 57 | +57 | 0 |
400 | 500 | +97 | 0 | 63 | +63 | 0 |
500 | 630 | +110 | 0 | 70 | +70 | 0 |
630 | 800 | +125 | 0 |
‒ |
+80 | 0 |
800 | 1 000 | +140 | 0 |
‒ |
+90 | 0 |
Tolerance symbols in accordance with ISO 492 ➤ Table
U = upper limit deviation
L = lower limit deviation
- Valid in any radial cross-section of the bore.
Tolerances for tapered bores, taper 1:30, tolerance class Normal
Nominal bore diameter |
Bore deviation |
Variation |
Deviation of taper slope |
|||
---|---|---|---|---|---|---|
d |
tΔdmp |
tVdsp1) |
tΔSL |
|||
mm |
μm |
μm |
μm |
|||
over |
incl. |
U |
L |
max. |
U |
L |
‒ |
80 | +15 | 0 | 19 | +35 | 0 |
80 | 120 | +20 | 0 | 25 | +40 | 0 |
120 | 180 | +25 | 0 | 31 | +50 | 0 |
180 | 250 | +30 | 0 | 38 | +55 | 0 |
250 | 315 | +35 | 0 | 44 | +60 | 0 |
315 | 400 | +40 | 0 | 50 | +65 | 0 |
400 | 500 | +45 | 0 | 56 | +75 | 0 |
500 | 630 | +50 | 0 | 63 | +85 | 0 |
630 | 800 | +75 | 0 |
‒ |
+100 | 0 |
800 | 1 000 | +100 | 0 |
‒ |
+100 | 0 |
Tolerance symbols in accordance with ISO 492 ➤ Table
U = upper limit deviation
L = lower limit deviation
- Valid in any radial cross-section of the bore.
Taper 1:12
Taper 1:12 is standardised
For rolling bearings with a tapered bore, the standardised taper is 1:12. This corresponds to a half taper angle (α/2 = 2°23′9,4″); basic taper angle α = 4°46′18,8″. An exception is spherical roller bearings of the dimension series 40, 41 and 42 (the taper in this case is 1:30).
For the dimensions and tolerances defined in ISO 492:2014 for a tapered bore ➤ Figure.
Tolerances for tapered bores Taper 1:12 d1 = d + 1/12 · B |
![]() |
Axial bearings
Bore diameter tolerances for shaft locating washers to ISO 199:2014
Nominal |
Tolerance class Normal, 6 and 5 |
Tolerance class 4 |
|||||
---|---|---|---|---|---|---|---|
Bore deviation |
Variation |
Bore deviation |
Variation |
||||
d |
tΔdmp |
tVdsp |
tΔdmp |
tVdsp |
|||
mm |
μm |
μm |
μm |
μm |
|||
over |
incl. |
U |
L |
max. |
U |
L |
max. |
‒ |
18 | 0 | –8 | 6 | 0 | –7 | 5 |
18 | 30 | 0 | –10 | 8 | 0 | –8 | 6 |
30 | 50 | 0 | –12 | 9 | 0 | –10 | 8 |
50 | 80 | 0 | –15 | 11 | 0 | –12 | 9 |
80 | 120 | 0 | –20 | 15 | 0 | –15 | 11 |
120 | 180 | 0 | –25 | 19 | 0 | –18 | 14 |
180 | 250 | 0 | –30 | 23 | 0 | –22 | 17 |
250 | 315 | 0 | –35 | 26 | 0 | –25 | 19 |
315 | 400 | 0 | –40 | 30 | 0 | –30 | 23 |
400 | 500 | 0 | –45 | 34 | 0 | –35 | 26 |
500 | 630 | 0 | –50 | 38 | 0 | –40 | 30 |
630 | 800 | 0 | –75 | 55 | 0 | –50 | 40 |
800 | 1000 | 0 | –100 | 75 | 0 |
‒ |
‒ |
1000 | 1250 | 0 | –125 | 95 | 0 |
‒ |
‒ |
Tolerance symbols in accordance with ISO 199 ➤ Table
U = upper limit deviation
L = lower limit deviation
Outside diameter tolerances for housing locating washers to ISO 199:2014
Nominal |
Tolerance class Normal, 6 and 5 |
Tolerance class 4 |
|||||
---|---|---|---|---|---|---|---|
Deviation |
Variation |
Deviation |
Variation |
||||
D |
tΔDmp |
tVDsp |
tΔDmp |
tVDsp |
|||
mm |
μm |
μm |
μm |
μm |
|||
over |
incl. |
U |
L |
max. |
U |
L |
max. |
10 | 18 | 0 | –11 | 8 | 0 | –7 | 5 |
18 | 30 | 0 | –13 | 10 | 0 | –8 | 6 |
30 | 50 | 0 | –16 | 12 | 0 | –9 | 7 |
50 | 80 | 0 | –19 | 14 | 0 | –11 | 8 |
80 | 120 | 0 | –22 | 17 | 0 | –13 | 10 |
120 | 180 | 0 | –25 | 19 | 0 | –15 | 11 |
180 | 250 | 0 | –30 | 23 | 0 | –20 | 15 |
250 | 315 | 0 | –35 | 26 | 0 | –25 | 19 |
315 | 400 | 0 | –40 | 30 | 0 | –28 | 21 |
400 | 500 | 0 | –45 | 34 | 0 | –33 | 25 |
500 | 630 | 0 | –50 | 38 | 0 | –38 | 29 |
630 | 800 | 0 | –75 | 55 | 0 | –45 | 34 |
800 | 1000 | 0 | –100 | 75 | 0 | –60 | 45 |
1000 | 1250 | 0 | –125 | 95 |
‒ |
‒ |
‒ |
1250 | 1600 | 0 | –160 | 120 |
‒ |
‒ |
‒ |
Tolerance symbols in accordance with ISO 199 ➤ Table
U = upper limit deviation
L = lower limit deviation
Variation in washer thickness for shaft and housing locating washers to ISO 199:2014
Nominal |
Tolerance class |
Tolerance class Normal, 6, 5, 4 |
||||
---|---|---|---|---|---|---|
d |
Normal |
6 |
5 |
4 |
||
Variation in thickness between shaft washer raceway and back face |
Variation in thickness between housing washer raceway and back face |
|||||
tSi |
tSe |
|||||
mm |
μm |
μm |
||||
over |
incl. |
max. |
max. |
|||
‒ |
18 | 10 | 5 | 3 | 2 |
Identical to tSi |
18 | 30 | 10 | 5 | 3 | 2 | |
30 | 50 | 10 | 6 | 3 | 2 | |
50 | 80 | 10 | 7 | 4 | 3 | |
80 | 120 | 15 | 8 | 4 | 3 | |
120 | 180 | 15 | 9 | 5 | 4 | |
180 | 250 | 20 | 10 | 5 | 4 | |
250 | 315 | 25 | 13 | 7 | 5 | |
315 | 400 | 30 | 15 | 7 | 5 | |
400 | 500 | 30 | 18 | 9 | 6 | |
500 | 630 | 35 | 21 | 11 | 7 | |
630 | 800 | 40 | 25 | 13 | 8 | |
800 | 1 000 | 45 | 30 | 15 |
‒ |
|
1 000 | 1 250 | 50 | 35 | 18 |
‒ |
Tolerance symbols in accordance with ISO 199 ➤ Table
Tolerances for nominal bearing height
Tolerances and symbols for nominal size
The tolerances for nominal height are given in ➤ Table. The corresponding symbols for nominal size are shown in ➤ Figure.
Nominal size symbols for nominal bearing height |
![]() |
Tolerances for nominal bearing height
Nominal |
tTs |
tT1s |
tT2s |
||||
---|---|---|---|---|---|---|---|
d |
|||||||
mm |
μm |
μm |
μm |
||||
over |
incl. |
U |
L |
U |
L |
U |
L |
‒ |
30 |
20 |
–250 |
100 |
–250 |
150 |
–400 |
30 |
50 |
20 |
–250 |
100 |
–250 |
150 |
–400 |
50 |
80 |
20 |
–300 |
100 |
–300 |
150 |
–500 |
80 |
120 |
25 |
–300 |
150 |
–300 |
200 |
–500 |
120 |
180 |
25 |
–400 |
150 |
–400 |
200 |
–600 |
180 |
250 |
30 |
–400 |
150 |
–400 |
250 |
–600 |
250 |
315 |
40 |
–400 |
200 |
–400 |
350 |
–700 |
315 |
400 |
40 |
–500 |
200 |
–500 |
350 |
–700 |
400 |
500 |
50 |
–500 |
300 |
–500 |
400 |
–900 |
500 |
630 |
60 |
–600 |
350 |
–600 |
500 |
–1 100 |
630 |
800 |
70 |
–750 |
400 |
–750 |
600 |
–1 300 |
800 |
1 000 |
80 |
–1 000 |
450 |
–1 000 |
700 |
–1 500 |
1 000 |
1 250 |
100 |
–1 400 |
500 |
–1 400 |
900 |
–1 800 |
continued ▼ |
Tolerance symbols in accordance with ISO 199 ➤ Table
U = upper limit deviation
L = lower limit deviation
Tolerances for nominal bearing height
Nominal |
tT3s |
tT4s |
|||
---|---|---|---|---|---|
d |
|||||
mm |
μm |
μm |
|||
over |
incl. |
U |
L |
U |
L |
‒ |
30 |
300 |
–400 |
20 |
–300 |
30 |
50 |
300 |
–400 |
20 |
–300 |
50 |
80 |
300 |
–500 |
20 |
–400 |
80 |
120 |
400 |
–500 |
25 |
–400 |
120 |
180 |
400 |
–600 |
25 |
–500 |
180 |
250 |
500 |
–600 |
30 |
–500 |
250 |
315 |
600 |
–700 |
40 |
–700 |
315 |
400 |
600 |
–700 |
40 |
–700 |
400 |
500 |
750 |
–900 |
50 |
–900 |
500 |
630 |
900 |
–1 100 |
60 |
–1 200 |
630 |
800 |
1 100 |
–1 300 |
70 |
–1 400 |
800 |
1 000 |
1 300 |
–1 500 |
80 |
–1 800 |
1000 |
1 250 |
1 600 |
–1 800 |
100 |
–2 400 |
continued ▲ |
Tolerance symbols in accordance with ISO 199 ➤ Table
U = upper limit deviation
L = lower limit deviation
Chamfer dimensions
Radial bearings, excluding tapered roller bearings
Minimum and maximum values
The minimum and maximum values for the bearings are given in the table Limit values for chamfer dimensions to DIN 620-6 ➤ Table, ➤ Figure.
For drawn cup needle roller bearings with open ends HK, drawn cup needle roller bearings with closed end BK and aligning needle roller bearings PNA and RPNA, the chamfer dimensions deviate from DIN 620-6. The lower limit values for r are given in the product tables.
Tapered roller bearings
Chamfer dimensions for tapered roller bearings ➤ Figure and ➤ Table, for axial bearings ➤ Figure and ➤ Table.
Chamfer dimensions for radial bearings (not including tapered roller bearings)
|
![]() |
Limit values for chamfer dimensions to DIN 620-6
r1) |
d |
r1 to r6a |
r1, r3, r5 |
r2, r4, r62) |
r4a, r6a |
|
---|---|---|---|---|---|---|
mm |
mm |
mm |
mm |
mm |
mm |
|
over |
incl. |
min. |
max. |
max. |
max. |
|
0,05 |
‒ |
‒ |
0,05 |
0,1 |
0,2 |
0,1 |
0,08 |
‒ |
‒ |
0,08 |
0,16 |
0,3 |
0,16 |
0,1 |
‒ |
‒ |
0,1 |
0,2 |
0,4 |
0,2 |
0,15 |
‒ |
‒ |
0,15 |
0,3 |
0,6 |
0,3 |
0,2 |
‒ |
‒ |
0,2 |
0,5 |
0,8 |
0,5 |
0,3 |
‒ |
40 |
0,3 |
0,6 |
1 |
0,8 |
0,3 |
40 |
‒ |
0,3 |
0,8 |
1 |
0,8 |
0,5 |
‒ |
40 |
0,5 |
1 |
2 |
1,5 |
0,5 |
40 |
‒ |
0,5 |
1,3 |
2 |
1,5 |
0,6 |
‒ |
40 |
0,6 |
1 |
2 |
1,5 |
0,6 |
40 |
‒ |
0,6 |
1,3 |
2 |
1,5 |
1 |
‒ |
50 |
1 |
1,5 |
3 |
2,2 |
1 |
50 |
‒ |
1 |
1,9 |
3 |
2,2 |
1,1 |
– |
120 |
1,1 |
2 |
3,5 |
2,7 |
1,1 |
120 |
‒ |
1,1 |
2,5 |
4 |
2,7 |
1,5 |
‒ |
120 |
1,5 |
2,3 |
4 |
3,5 |
1,5 |
120 |
‒ |
1,5 |
3 |
5 |
3,5 |
2 |
‒ |
80 |
2 |
3 |
4,5 |
4 |
2 |
80 |
220 |
2 |
3,5 |
5 |
4 |
2 |
220 |
‒ |
2 |
3,8 |
6 |
4 |
2,1 |
‒ |
280 |
2,1 |
4 |
6,5 |
4,5 |
2,1 |
280 |
‒ |
2,1 |
4,5 |
7 |
4,5 |
2,5 |
‒ |
100 |
2,5 |
3,8 |
6 |
5 |
2,5 |
100 |
280 |
2,5 |
4,5 |
6 |
5 |
2,5 |
280 |
‒ |
2,5 |
5 |
7 |
5 |
3 |
‒ |
280 |
3 |
5 |
8 |
5,5 |
3 |
280 |
‒ |
3 |
5,5 |
8 |
5,5 |
4 |
‒ |
‒ |
4 |
6,5 |
9 |
6,5 |
5 |
‒ |
‒ |
5 |
8 |
10 |
8 |
6 |
‒ |
‒ |
6 |
10 |
13 |
10 |
7,5 |
‒ |
‒ |
7,5 |
12,5 |
17 |
12,5 |
9,5 |
‒ |
‒ |
9,5 |
15 |
19 |
15 |
12 |
‒ |
‒ |
12 |
18 |
24 |
18 |
15 |
‒ |
‒ |
15 |
21 |
30 |
21 |
19 |
‒ |
‒ |
19 |
25 |
38 |
25 |
- The nominal chamfer dimension r is identical to the smallest permissible chamfer dimension rmin.
- For bearings with a width of 2 mm or less, the values for r1 apply.
Tapered roller bearings
Minimum and maximum values
Minimum and maximum values for metric tapered roller bearings ➤ Figure and ➤ Table.
Chamfer dimensions for metric tapered roller bearings |
![]() |
Limit values for chamfer dimensions
r1) |
d, D |
r1 to r4 |
r1, r3 |
r2, r4 |
|
---|---|---|---|---|---|
mm |
mm |
mm |
mm |
mm |
|
over |
incl. |
min. |
max. |
max. |
|
0,3 |
‒ |
40 | 0,3 | 0,7 | 1,4 |
0,3 | 40 |
‒ |
0,3 | 0,9 | 1,6 |
0,6 | ‒ | 40 | 0,6 | 1,1 | 1,7 |
0,6 | 40 |
‒ |
0,6 | 1,3 | 2 |
1 |
‒ |
50 | 1 | 1,6 | 2,5 |
1 | 50 |
‒ |
1 | 1,9 | 3 |
1,5 |
‒ |
120 | 1,5 | 2,3 | 3 |
1,5 | 120 | 250 | 1,5 | 2,8 | 3,5 |
1,5 | 250 |
‒ |
1,5 | 3,5 | 4 |
2 |
‒ |
120 | 2 | 2,8 | 4 |
2 | 120 | 250 | 2 | 3,5 | 4,5 |
2 | 250 |
‒ |
2 | 4 | 5 |
2,5 |
‒ |
120 | 2,5 | 3,5 | 5 |
2,5 | 120 | 250 | 2,5 | 4 | 5,5 |
2,5 | 250 |
‒ |
2,5 | 4,5 | 6 |
3 |
‒ |
120 | 3 | 4 | 5,5 |
3 | 120 | 250 | 3 | 4,5 | 6,5 |
3 | 250 | 400 | 3 | 5 | 7 |
3 | 400 |
‒ |
3 | 5,5 | 7,5 |
4 |
‒ |
120 | 4 | 5 | 7 |
4 | 120 | 250 | 4 | 5,5 | 7,5 |
4 | 250 | 400 | 4 | 6 | 8 |
4 | 400 |
‒ |
4 | 6,5 | 8,5 |
5 |
‒ |
180 | 5 | 6,5 | 8 |
5 | 180 |
‒ |
5 | 7,5 | 9 |
6 |
‒ |
180 | 6 | 7,5 | 10 |
6 | 180 |
‒ |
6 | 9 | 11 |
- The nominal chamfer dimension r is identical to the smallest permissible chamfer dimension rmin.
Axial bearings
Minimum and maximum values
Minimum and maximum values for the bearings ➤ Figure and ➤ Table. The values in the table correspond to DIN 620-6. In the case of axial deep groove ball bearings, the tolerances for the chamfer dimensions are identical in both axial and radial directions.
Chamfer dimensions for axial bearings
|
![]() |
Limit values for chamfer dimensions
r1) |
r1, r2 |
|
---|---|---|
mm |
mm |
mm |
min. |
max. |
|
0,05 | 0,05 | 0,1 |
0,08 | 0,08 | 0,16 |
0,1 | 0,1 | 0,2 |
0,15 | 0,15 | 0,3 |
0,2 | 0,2 | 0,5 |
0,3 | 0,3 | 0,8 |
0,6 | 0,6 | 1,5 |
1 | 1 | 2,2 |
1,1 | 1,1 | 2,7 |
1,5 | 1,5 | 3,5 |
2 | 2 | 4 |
2,1 | 2,1 | 4,5 |
3 | 3 | 5,5 |
4 | 4 | 6,5 |
5 | 5 | 8 |
6 | 6 | 10 |
7,5 | 7,5 | 12,5 |
9,5 | 9,5 | 15 |
12 | 12 | 18 |
15 | 15 | 21 |
19 | 19 | 25 |
- The nominal chamfer dimension r is identical to the smallest permissible chamfer dimension rmin.