Customer Success Story
Quick & Easy Setup - Immediate Failure Identification
Lehigh Hanson was not satisfied with the existing once-per-month condition-monitoring schedule for the critical machines at its facility in Union Bridge, Md. Because unplanned downtime needs to be detected as early as possible, the cement manufacturer opted for Schaeffler’s award-winning OPTIME wireless condition monitoring solution. This consequential decision quickly paid off: Shortly after the first sensors were installed, OPTIME reported a potential problem with a cooling fan.
Preventing this one unplanned shutdown alone saved Lehigh Hanson approximately 15,000 US dollars.
Benefits
Customer benefits
Quick and easy installation of OPTIME components.
Data is easy to read and understand – no expert knowledge required.
Improved safety for employees – wireless sensors eliminate the need to access hard-to-reach machinery.
Cost-effective solution for comprehensive monitoring of assets.
Permits long-term planning of maintenance measures, personnel requirements and spare parts procurement.
Unplanned downtime is no longer an issue for monitored machines.
Challenge
Lehigh Hanson has been supplying cement, aggregates, ready-mix concrete, asphalt and other building materials to customers throughout North America for more than a century. Union Bridge is the company’s largest cement plant operating in the region. A typical cement manufacturing process involves crushing, sizing and mixing inputs such as limestone and clay to create the raw material that is then ground in grinding mills and heated in a rotary kiln to temperatures as high as 1450 °C. The resulting material that leaves the kiln is known as “clinker,” which is ground again to a fine powder ...which we know as cement. Unplanned shutdowns are very costly in the cement-making business.
My greatest worry is an unplanned shutdown of the plant. Up to now, we had a service provider monitor the machines and evaluate the data. Unfortunately, some failures were not detected by their system. Our clinker cooler fans are a critical part of our operation,
says Carmelo Hernandez, Maintenance Manager
This is why the Lehigh Hanson maintenance manager was seeking a solution that a) would provide early insight into the health of the machinery, and b) could be accessed automatically by maintenance personnel. Accordingly, Lehigh Hanson turned to Schaeffler.Solution
The experts at Schaeffler recommended their award-winning OPTIME condition monitoring solution. This scalable system consists of wireless sensors, a cellular gateway and digital services that are based on proprietary Schaeffler algorithms. A pilot project at Lehigh Hanson’s Union Bridge facility involved installing ten OPTIME sensors and a gateway. Shortly after installation, a warning of impending bearing damage to the facility’s E03-019 cooling fan was displayed on the OPTIME app.
Lehigh Hanson confirmed the issue after an inspection: A spherical roller bearing housing was cocked, which caused the temperature to rise. The problem was corrected and, for a short period of time, the values of the cooling fan moved within the normal range. After about two months, however, another warning message appeared on the same fan. This time, the maintenance manager contacted the Schaeffler experts directly. They performed an indepth analysis using OPTIME’s ExpertViewer* tool. As a result, a defect on the outer ring of the previously cocked bearing was detected. The issue was quickly addressed by the maintenance team, and an unplanned shutdown was avoided.
How OPTIME works
What’s special
I am thrilled that technology, packaging and pricing have finally come together to make a solution like OPTIME possible – and easily financially justifiable.
says Carmelo Hernandez, Maintenance Manager, Lehigh Hanson, HeidelbergCement Group
Savings
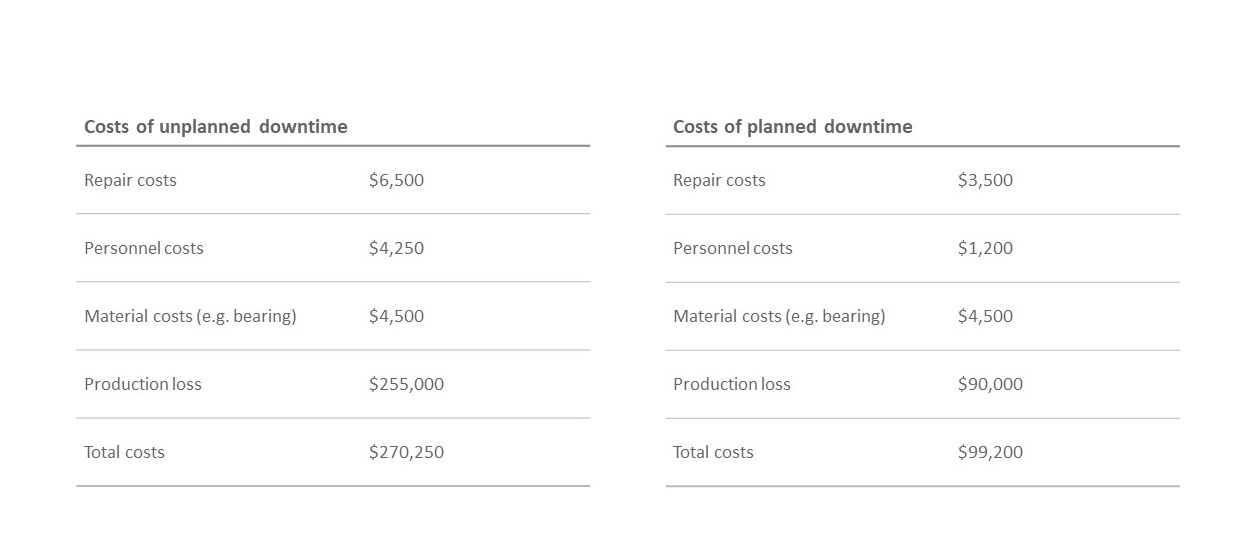